See now the technique of soldering iron on thin boxes to avoid punctures that not everyone knows
Galvanized box iron is a popular material in many projects thanks to its durability and good oxidation resistance. However, when welding this type of material, especially thin plates, if not done correctly, it can easily cause punctures, affecting the weld quality and structural durability.
Contents
So how can you weld galvanized square steel tubing without burning through? To prevent burn-through, it is crucial to control the temperature, select the appropriate welding electrode or wire, and apply the correct welding technique. Below, EMIN will share the proper welding methods for galvanized square steel tubing to avoid burn-through and ensure the best weld quality.
Why does the soldering iron on a thin box get punctured?
For less experienced welders, burning through galvanized square steel tubing is a common issue, and in my observation, it happens quite frequently. The main reason often comes from selecting a welding electrode with too large a diameter or using excessively high welding current, causing the heat to concentrate at the weld point beyond the material's tolerance.
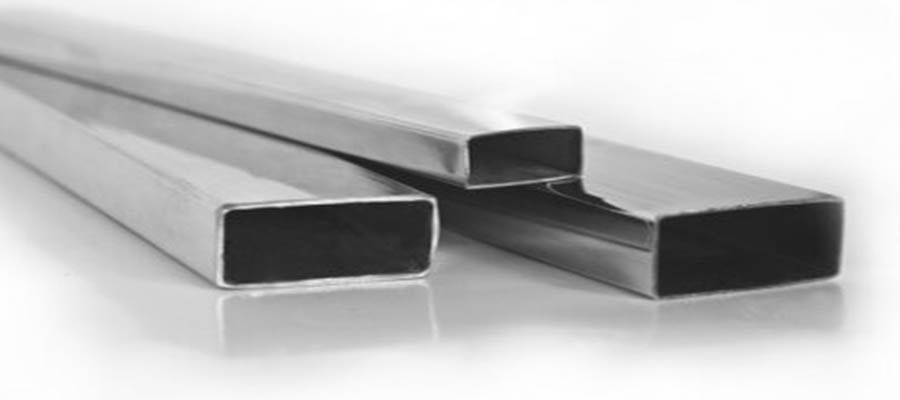
Additionally, holding the arc in one spot for too long can also cause thin-walled tubing to burn through, compromising the weld quality.
To minimize this issue, welders typically choose electrodes with a smaller diameter that match the material thickness. At the same time, adjusting the welding current to a lower level helps control heat input, preventing warping or damage to the weld surface. When the correct technique is applied, the weld bead will be uniform and of high quality.
What to note before welding?
To create a strong and aesthetically pleasing weld, it is essential to select an electrode with an appropriate diameter and adjust the welding current according to the material's thickness. Additionally, the welder's skill level, combined with the welding machine's performance, plays a crucial role in determining weld quality.
When using stick welding, it is recommended to apply an intermittent welding technique rather than maintaining the arc in one spot for too long, as this can easily burn through the material—especially when working with galvanized or thin-walled steel tubing.
For these materials, the welding stop-start motion should be slower than when welding thicker materials to better control heat input and prevent overheating, which could lead to deformation or burn-through of the weld surface.
Related articles:
Weld thick iron with a stick welder to make the weld beautiful
Laser welding technology and things to keep in mind when using laser welding machines
Principle of welding thin iron without punctures
Here are some essential principles to follow before welding thin steel to prevent burn-through:
When welding steel tubing with a stick welding machine, although surface cleaning is not highly demanding, it remains crucial to ensure a strong and even weld. Use a steel brush or specialized cleaning tools to remove dust and debris. Additionally, the area where the ground clamp is placed should be cleaned thoroughly to ensure good contact, helping to stabilize the arc during welding.
Proper welding posture is also important for better visibility of the weld pool and improved control over the weld bead. Choose an optimal viewing angle, avoid blocking your line of sight with your hands, and take precautions to minimize inhalation of harmful fumes generated during the welding process to protect your health.
What are some ways to solder iron boxes without punctures?
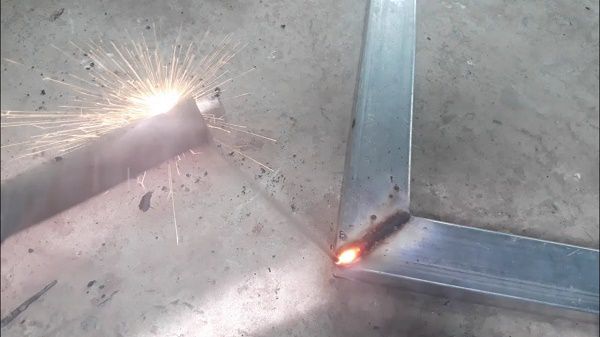
Set the appropriate current
Before starting the welding process, it is essential to set the correct type of current according to the electrode requirements, whether it is direct current electrode positive (DCEP), direct current electrode negative (DCEN), or alternating current (AC). Proper setup from the beginning ensures a stable welding process and prevents technical errors.
The welding current should be adjusted based on the electrode diameter and type. Typically, these specifications are provided on the electrode packaging, allowing you to set the appropriate current accordingly. Additionally, a basic reference calculation is that 1 Amp corresponds to approximately 0.0254 mm of electrode diameter.
For beginners, to prevent burning through thin steel tubing, it is advisable to start with a low welding current and gradually increase it by 5 to 10 Amps until reaching the optimal setting. Proper current control from the start will help produce clean, strong welds without damaging the material.
Adjust arc length
Arc length directly affects weld quality. When welding thin tins, make sure the arc length does not exceed the diameter of the welding rod to avoid puncturing the material.
If the arc is too short, it will be unstable, easily extinguished, cause the weld puddle to freeze quickly and may create unwanted weld flakes.
If the arc is too long, spatter will increase, the precipitation rate will slow, and porosity will easily occur, reducing weld quality.
Adjust the welding rod angle appropriately
The welding angle plays a crucial role in controlling the weld quality. When welding thin steel tubing with an arc welding machine:
- For horizontal welding, the electrode should be held at an angle of 5 to 15 degrees in the direction of movement.
- For vertical welding, the electrode angle can be adjusted between 0 and 15 degrees, tilted opposite to the welding direction to ensure a more stable weld.
Welding rod movement
Depending on the thickness of the material, you can use different welding movements such as horizontal, continuous, or intermittent welding. However, when welding thin steel tubing, lateral movement is unnecessary, as the arc width is sufficient to create the weld groove. Maintaining a steady movement along the weld axis helps control arc length effectively, resulting in a cleaner and stronger weld.